richiewillmott
New Member
Hi,
I'm looking for some help on this Adjustable SMPS Circuit found on Danyk.cz,
I've built the circuit on a PCB and everything works fine Voltage regulation etc...
But as soon as I attach a load (A 60 Watt 12V Light Bulb) in this case, the IGBTs short out and die, all 3 legs are shorted together.
I tried with 600v Mosfets as well but the same still happens.
It's not on the PCB I designed, but I have soldered RC Snubbers accross the IGBTs
Any Help would be much appreciated.
I'm looking for some help on this Adjustable SMPS Circuit found on Danyk.cz,
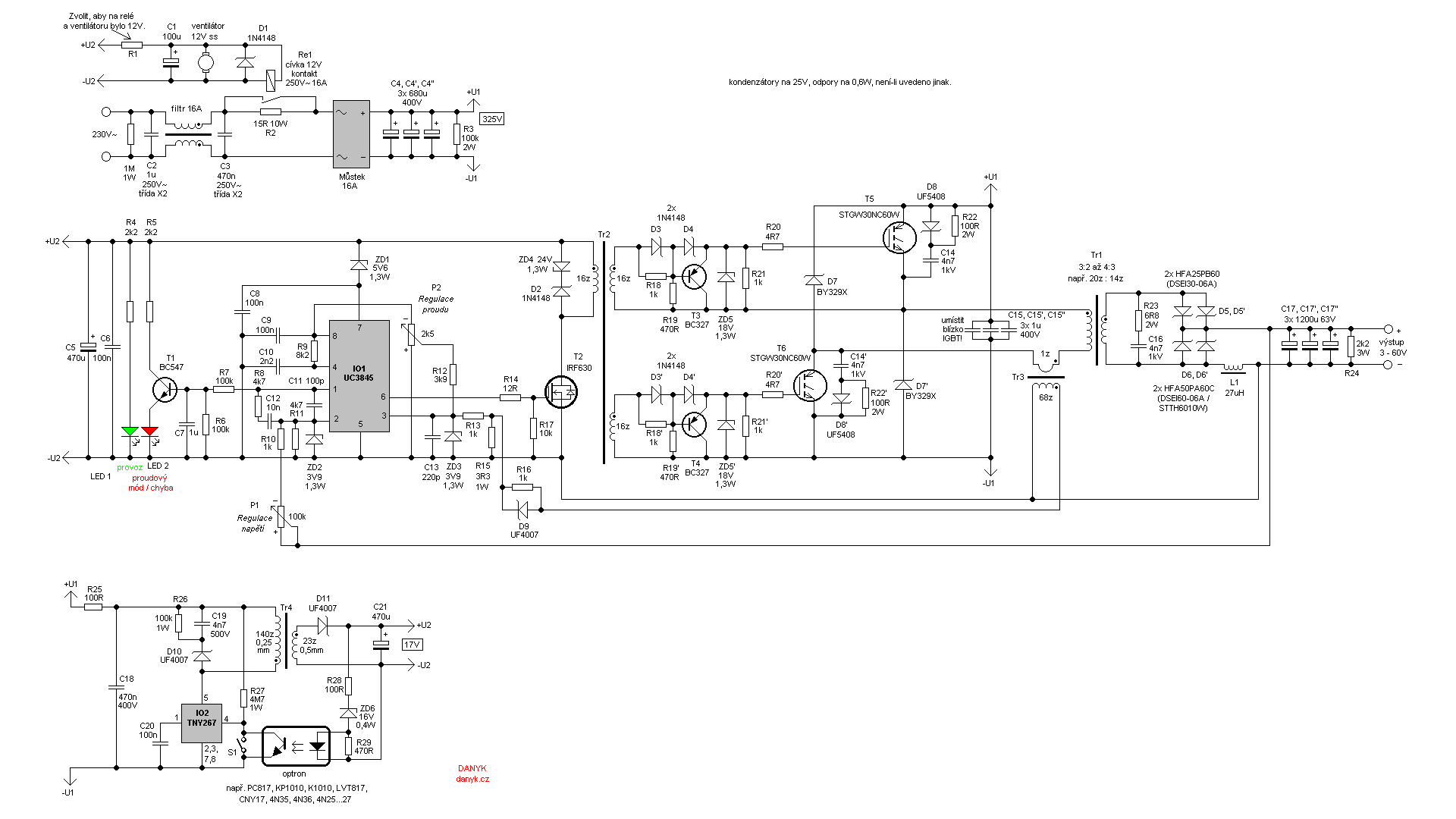
I've built the circuit on a PCB and everything works fine Voltage regulation etc...
But as soon as I attach a load (A 60 Watt 12V Light Bulb) in this case, the IGBTs short out and die, all 3 legs are shorted together.
I tried with 600v Mosfets as well but the same still happens.
It's not on the PCB I designed, but I have soldered RC Snubbers accross the IGBTs

Any Help would be much appreciated.