Alexanderfitu
New Member
Hi all
First of all, I have always been a tinkerer, but never properly understood the more complicated electrical circuits.
Anywho, I am trying drive a tachometer, that takes 12v pulses from a compression ignition engine (therefore no spark ignition to measure RPM).
My idea is to have a Magnet on the flywheel, then a proximity sensor feeding 12v to the tach when the magnet passes by.
The proximity sensor I am going to use is a Cherry Mp1013:
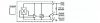
This shows it needs a pull up resistor between VCC and Ground. based on a 13V input voltage, what resistor would I need.
Can anybody confirm that my circuit diag here isnt completely wrong
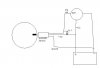
Thanks in advance

First of all, I have always been a tinkerer, but never properly understood the more complicated electrical circuits.
Anywho, I am trying drive a tachometer, that takes 12v pulses from a compression ignition engine (therefore no spark ignition to measure RPM).
My idea is to have a Magnet on the flywheel, then a proximity sensor feeding 12v to the tach when the magnet passes by.
The proximity sensor I am going to use is a Cherry Mp1013:
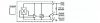
This shows it needs a pull up resistor between VCC and Ground. based on a 13V input voltage, what resistor would I need.
Can anybody confirm that my circuit diag here isnt completely wrong
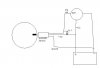
Thanks in advance