easy.rahil
Member
hello experts,
i m trying to make an electronic ignition like pamco and got similar design from a friend, i make homemade pcb for this schematic but output is coming without using magnet(added an led to check output and its constant on). can anyone guide me?
PCB
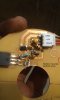
I m using MLX90217 geartooth sensor in place of A1250 Hall sensor.
U1 is IRGB14C40L mosfet.
Also let me know if there is any other hall sensor i can use
please let me know what is the actual problem
i m trying to make an electronic ignition like pamco and got similar design from a friend, i make homemade pcb for this schematic but output is coming without using magnet(added an led to check output and its constant on). can anyone guide me?
PCB
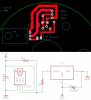
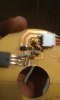
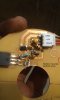
I m using MLX90217 geartooth sensor in place of A1250 Hall sensor.
U1 is IRGB14C40L mosfet.
Also let me know if there is any other hall sensor i can use
please let me know what is the actual problem