ADWSystems
Member
As I previously posted, I'm interested in building a circuit to test NiCad batteries. The testing will be focused cell by cell to weed out or combine like power cells, and junk the bad ones. From the information that I have been able to find (especially since I was able to find several battery tester threads when I didn't search for NiCad), the battery should be discharge at 1/10 mAHr Capacity to 1.0 and never below 0.8. This applies to a single cell. Can this be directly extrpolated to the multi-cell packs, such that one should discharge a 9.6V 8cell pack to 8.0V and never below 6.4V, etc.?
From this thread, https://www.electro-tech-online.com/threads/battery-tester-help-needed-thanks.7232/ I have come up with this circuit and appears to simulate quite well.
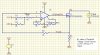
From this thread, https://www.electro-tech-online.com/threads/battery-tester-help-needed-thanks.7232/ I have come up with this circuit and appears to simulate quite well.
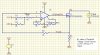