Since many of you have been patiently waiting for a new and more complete GTI design I figured I would give you some new schematics for a slightly more advanced system to think about for a while. 
This is in a way a continuation of the first Grid Tie Inverter Schematic thread from last year so I will not be going over everything in fine detail immediately regarding the operation and function of the exact circuits. Nor am I going to spend much time regarding the defense and argument of what is legal, illegal, safe, or unsafe in any country, location, or personal application relating to experience or inexperience by any individual. To that end here is my general liability statement pertaining to the issues the arm chair safety Nazis seem to continually have so much trouble dealing with.
This GTI build up Thread is intended for conceptual purposes and does implement live line power level voltages in some parts of the circuits which if mishandled can injure and or kill. Should you decide to build and use such a device based on this or other GTI schematics I or anyone else has provided freely on the internet you yourself are liable for your accidents, injures, property damage, and other unforeseen happenings that may negatively affect, injure or possibly kill yourself or others due to your choice to attempt to build and use such a device.
By building such device as these schematics pertain to in original or modified form you may be breaking laws and could be subject to possible fines, jail, and or prison time for it.
Should you choose to build such a device as this and intend to use it for saving energy in your home or dwelling you may very well be breaking the law. Beware by building and using such a system you will be deemed a pirate cogeneration operator which is considered illegal in many countries!
Basically this means you have to be proficient enough at understanding schematics and electrical and electronics principles to be able to safely build and fine tune a design or circuit such as this and adapt it to your specific needs required for your location and get away with using it as well. What you do with information you find on line and how you apply or misuse it is basically not my problem.
Once again this is a “conceptual circuit” lacking the full safety interlocks and other features that a full legal system would have and use. However when built properly this circuit is a fully functional GTI system based on an exact circuit design I have been using successfully for years now in multiple GTI’s of greatly varying power handling capacities I have built over the years. These as drawn schematics however do not show the various indicator LED’s in place that normally indicate when specific components are on or off on the real as built GTI units I use them in.
The first schematic, ‘Power handling circuit.’ is the high current higher voltage power handling system which is based on a standard H bridge design. In this application the IGBT’s are driven from actual driver IC’s and not a small control transformers as was shown in the old thread. By using the driver IC’s a more precise zero crossing point timing and switching device efficiency is possible which also improves the overall performance and control of the system. This also gives the greater advantages of being able to manipulate the waveforms in different ways relating to additional current and voltage control feedback circuits that can be used to protect and limit the power that may be applied to the GTI power handling systems as well. As you will note there are multiple lines, [To (A)] through [To (K)], running to different control circuits not shown in the ‘Power handling circuit’ schematic. They relate to the ‘Control circuit A’ schematic and an optional ‘Control circuit B’ schematic which specifically handles the higher level safety interlock functions. Plus there is a ‘Control circuit C’ schematic which adds full PWM waveform shaping and further current control capabilities plus external interface functions as well.
The ‘Power handling circuit’ and the ‘Control circuit A’ are the basic systems that will allow for full operation, with limited system protection, of this type of GTI system. The other two control circuits are the extra support systems needed for additional features but are not essential to the basic system operation and will not likely be covered any time soon. However if built properly this more basic design does allow for them to be added on at any time by simple plug and play additions.
Unfortunately I am not sure how quickly I will be able to get to doing the more in depth descriptive write ups on this GTI design being I have been hired to drive truck in the oil fields and work long hours. For me this is a low priority hobby project of mine and nothing else. You will get what I give when I have time to give it. this may be a better schematic and system design than the first one I gave out last year but unfortunately you will still have to think a bit more if you choose to use it.
If your electronics skills are good you will be able to work out what everything does and why it is needed. This circuit is highly adaptable and can be used with any input voltage and current within the working ranges of the components chosen, It can adapted to work on a low voltage low current system that can work with as little as a few tens of watts from a 12 volt based system up to that multi kilowatt capacity system that run at inputs of up to around 400 volts and over 100 amps. The adaptability comes from the design only needing a few changes in the sizing of a few specific components. There are only a few capacitors, resistors, diodes, switching devices, plus the power transformer and its related line side post filtering circuit that determine what voltage and current capacity this circuit can effectively work on.

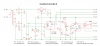
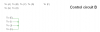

This is in a way a continuation of the first Grid Tie Inverter Schematic thread from last year so I will not be going over everything in fine detail immediately regarding the operation and function of the exact circuits. Nor am I going to spend much time regarding the defense and argument of what is legal, illegal, safe, or unsafe in any country, location, or personal application relating to experience or inexperience by any individual. To that end here is my general liability statement pertaining to the issues the arm chair safety Nazis seem to continually have so much trouble dealing with.

This GTI build up Thread is intended for conceptual purposes and does implement live line power level voltages in some parts of the circuits which if mishandled can injure and or kill. Should you decide to build and use such a device based on this or other GTI schematics I or anyone else has provided freely on the internet you yourself are liable for your accidents, injures, property damage, and other unforeseen happenings that may negatively affect, injure or possibly kill yourself or others due to your choice to attempt to build and use such a device.
By building such device as these schematics pertain to in original or modified form you may be breaking laws and could be subject to possible fines, jail, and or prison time for it.
Should you choose to build such a device as this and intend to use it for saving energy in your home or dwelling you may very well be breaking the law. Beware by building and using such a system you will be deemed a pirate cogeneration operator which is considered illegal in many countries!
Basically this means you have to be proficient enough at understanding schematics and electrical and electronics principles to be able to safely build and fine tune a design or circuit such as this and adapt it to your specific needs required for your location and get away with using it as well. What you do with information you find on line and how you apply or misuse it is basically not my problem.

Once again this is a “conceptual circuit” lacking the full safety interlocks and other features that a full legal system would have and use. However when built properly this circuit is a fully functional GTI system based on an exact circuit design I have been using successfully for years now in multiple GTI’s of greatly varying power handling capacities I have built over the years. These as drawn schematics however do not show the various indicator LED’s in place that normally indicate when specific components are on or off on the real as built GTI units I use them in.
The first schematic, ‘Power handling circuit.’ is the high current higher voltage power handling system which is based on a standard H bridge design. In this application the IGBT’s are driven from actual driver IC’s and not a small control transformers as was shown in the old thread. By using the driver IC’s a more precise zero crossing point timing and switching device efficiency is possible which also improves the overall performance and control of the system. This also gives the greater advantages of being able to manipulate the waveforms in different ways relating to additional current and voltage control feedback circuits that can be used to protect and limit the power that may be applied to the GTI power handling systems as well. As you will note there are multiple lines, [To (A)] through [To (K)], running to different control circuits not shown in the ‘Power handling circuit’ schematic. They relate to the ‘Control circuit A’ schematic and an optional ‘Control circuit B’ schematic which specifically handles the higher level safety interlock functions. Plus there is a ‘Control circuit C’ schematic which adds full PWM waveform shaping and further current control capabilities plus external interface functions as well.
The ‘Power handling circuit’ and the ‘Control circuit A’ are the basic systems that will allow for full operation, with limited system protection, of this type of GTI system. The other two control circuits are the extra support systems needed for additional features but are not essential to the basic system operation and will not likely be covered any time soon. However if built properly this more basic design does allow for them to be added on at any time by simple plug and play additions.
Unfortunately I am not sure how quickly I will be able to get to doing the more in depth descriptive write ups on this GTI design being I have been hired to drive truck in the oil fields and work long hours. For me this is a low priority hobby project of mine and nothing else. You will get what I give when I have time to give it. this may be a better schematic and system design than the first one I gave out last year but unfortunately you will still have to think a bit more if you choose to use it.
If your electronics skills are good you will be able to work out what everything does and why it is needed. This circuit is highly adaptable and can be used with any input voltage and current within the working ranges of the components chosen, It can adapted to work on a low voltage low current system that can work with as little as a few tens of watts from a 12 volt based system up to that multi kilowatt capacity system that run at inputs of up to around 400 volts and over 100 amps. The adaptability comes from the design only needing a few changes in the sizing of a few specific components. There are only a few capacitors, resistors, diodes, switching devices, plus the power transformer and its related line side post filtering circuit that determine what voltage and current capacity this circuit can effectively work on.

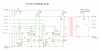
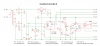
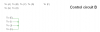
Last edited: