Some time ago I tackled the concept of how to build a complete and functioning yet simple all analog based Grid Tie Inverter, GTI, that could be built out of common parts and salvaged components so to further expand on the theme of low price recycle AE tech I came up with a fairly simple and strait forward design for a full PWM sine wave power inverter that can also be built out of second hand parts and pieces with little more than two 555 timers, a LM1458 op amp, and a IRF2110 IGBT/Mosfet driver IC.
The point and purpose of this design is to put a defined answer to that never ending question that every electronics forum sees almost every single day which we all know as, 'Please sirs I have need for 555 sine wave inverter circuit' or something to that effect. So to answer that never ending question here is a complete yet basic 555 timer IC based pulse width shaped sine wave power inverter schematic that is adaptable to almost any range of input and output voltages and power levels while still being buildable from basic common parts.
The basic principal behind this design is that the common 555 timer IC can operate in a number of different modes with only a few additional resistors and capacitors in order to serve in a wide range of functions and applications. In this circuit the two 555 timer IC’s are working together to produce two base frequency wave forms which are added together in the LM1458 Op amp IC resulting a 50 or 60 Hz PWM shaped sine wave superimposed on a 30KHz base switching frequency.
In order to produce a high frequency PWM signal that can be widely varied from 0 to 100% duty cycle with a 50 or 60 Hz sine wave superimposed on it the U1 555 timer IC set up to produce a constant 50% duty cycle 30 KHz square wave. That 50% duty cycle square wave gets passed through a simple RC filter that reshapes it into a symmetrical triangle wave. From there that signal is then fed to the negative input of U3b which is set up in a standard comparator configuration where the 30 KHZ signal is used to create a steady 30 KHz square wave that can now be fully modulated from 0 to 100% duty cycle by varying the voltage on the positive input of the comparator.
To produce the 50 or 60 Hz sine wave with the U2 555 timer IC the normal square wave output is reshaped into an approximated sine wave by passing it through a pair of simple RC low pass filters. In the first filter stage it gets reshaped from the square wave to a symmetrical triangle wave where it then can be passed onto the second stage that further reshapes the triangle wave into the approximated sine wave which is what gets fed to the positive input pin of the LM1458 U3a IC. The LM1458 U3a op amp is working as part of a voltage feedback loop that varies and stabilizes the gain of the system so that a basic but fairly effective automatic voltage regulation can be performed.
By combining the two different signals in the LM1458 U3b two fixed duty cycle signals are able to be turned into a PWM shaped sine wave that is based on the 30 KHZ a carrier frequency and the superimposed 50 or 60 Hz sine wave approximation.
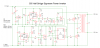
Click on thumbnail for full size view.
The point and purpose of this design is to put a defined answer to that never ending question that every electronics forum sees almost every single day which we all know as, 'Please sirs I have need for 555 sine wave inverter circuit' or something to that effect. So to answer that never ending question here is a complete yet basic 555 timer IC based pulse width shaped sine wave power inverter schematic that is adaptable to almost any range of input and output voltages and power levels while still being buildable from basic common parts.
The basic principal behind this design is that the common 555 timer IC can operate in a number of different modes with only a few additional resistors and capacitors in order to serve in a wide range of functions and applications. In this circuit the two 555 timer IC’s are working together to produce two base frequency wave forms which are added together in the LM1458 Op amp IC resulting a 50 or 60 Hz PWM shaped sine wave superimposed on a 30KHz base switching frequency.
In order to produce a high frequency PWM signal that can be widely varied from 0 to 100% duty cycle with a 50 or 60 Hz sine wave superimposed on it the U1 555 timer IC set up to produce a constant 50% duty cycle 30 KHz square wave. That 50% duty cycle square wave gets passed through a simple RC filter that reshapes it into a symmetrical triangle wave. From there that signal is then fed to the negative input of U3b which is set up in a standard comparator configuration where the 30 KHZ signal is used to create a steady 30 KHz square wave that can now be fully modulated from 0 to 100% duty cycle by varying the voltage on the positive input of the comparator.
To produce the 50 or 60 Hz sine wave with the U2 555 timer IC the normal square wave output is reshaped into an approximated sine wave by passing it through a pair of simple RC low pass filters. In the first filter stage it gets reshaped from the square wave to a symmetrical triangle wave where it then can be passed onto the second stage that further reshapes the triangle wave into the approximated sine wave which is what gets fed to the positive input pin of the LM1458 U3a IC. The LM1458 U3a op amp is working as part of a voltage feedback loop that varies and stabilizes the gain of the system so that a basic but fairly effective automatic voltage regulation can be performed.
By combining the two different signals in the LM1458 U3b two fixed duty cycle signals are able to be turned into a PWM shaped sine wave that is based on the 30 KHZ a carrier frequency and the superimposed 50 or 60 Hz sine wave approximation.
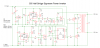
Click on thumbnail for full size view.
Last edited: