Triode
Well-Known Member
I'm trying to figure out why my motor driver doesn't like a 90% duty cycle. It works fine at 0-80 and 100, but at 90 it gets hot. I've found that the gate driver is lowering it's duty cycle at that range. I don't know why. More details and traces below.
I'm using an IR2136 driver
https://www.infineon.com/dgdl/ir2136.pdf?fileId=5546d462533600a4015355c8a02116a5
and the transistors are IRFB7430
https://www.infineon.com/dgdl/irfb7430pbf.pdf?fileId=5546d462533600a4015356169bcd1e53
Here's my circuit
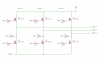
The motor being driven is 0.3 ohms through any pair of leads. Controller is a PSoC, set up to do PWM on the high side. The commutation table seems to work well so unless requested I'm going to skip that whole schematic and code.
Now here is the issue, at 90% duty cycle it gets very hot. It's fine at 0 to 80 and at 100, just not 90. I found a trace that at least seems to point to the reason why. If anyone is so kind as to help I'll be glad to get other current or voltage traces as needed. I can do up to 3 current traces and 4 voltages at once. The following traces are of the gate voltage coming from the driver chip. At 30% and 80% they're fine, close to the expected duty cycle, at 100% (not shown) it's just a plateau as you would expect. But at 90% it's not nearly 90%, closer to 60%.
Details
PWM f = 20kHz
FET positive supply 14.8-14.6V from a lipo battery
Driver chip supply 17.4V from a 10A current limited power supply
30% - the top trace is the one of interest, the lower one is just me monitoring the low side gate, as expected it stayed near 0.
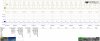
80% - note on this one the motor moved, so the lower part at the start is not the full signal, seems like it should be 0 though not a lower pulse.
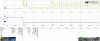
90%

Any ideas?
Thanks for any help!
I'm using an IR2136 driver
https://www.infineon.com/dgdl/ir2136.pdf?fileId=5546d462533600a4015355c8a02116a5
and the transistors are IRFB7430
https://www.infineon.com/dgdl/irfb7430pbf.pdf?fileId=5546d462533600a4015356169bcd1e53
Here's my circuit
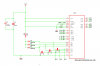
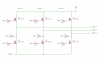
The motor being driven is 0.3 ohms through any pair of leads. Controller is a PSoC, set up to do PWM on the high side. The commutation table seems to work well so unless requested I'm going to skip that whole schematic and code.
Now here is the issue, at 90% duty cycle it gets very hot. It's fine at 0 to 80 and at 100, just not 90. I found a trace that at least seems to point to the reason why. If anyone is so kind as to help I'll be glad to get other current or voltage traces as needed. I can do up to 3 current traces and 4 voltages at once. The following traces are of the gate voltage coming from the driver chip. At 30% and 80% they're fine, close to the expected duty cycle, at 100% (not shown) it's just a plateau as you would expect. But at 90% it's not nearly 90%, closer to 60%.
Details
PWM f = 20kHz
FET positive supply 14.8-14.6V from a lipo battery
Driver chip supply 17.4V from a 10A current limited power supply
30% - the top trace is the one of interest, the lower one is just me monitoring the low side gate, as expected it stayed near 0.
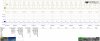
80% - note on this one the motor moved, so the lower part at the start is not the full signal, seems like it should be 0 though not a lower pulse.
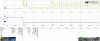
90%

Any ideas?
Thanks for any help!
Last edited: