polashd
Member
I've made the circuit (attached) to produce signal to drive my BLDC ESC. In Ltspice it shows producing required signal, almost (50 Hz, duty 5% to 10%) with the variable R (R5=10k).
But when I made and tested it practically the ESC (& motor) not running giving err tone. I tested with DMM and found frequency and duty% far from what was demonstrated in Ltspice. I did some trial and err using different values for R1, R2 & C2, finally reached a point where it is working but the running of the motor is not smooth enough.
I want to use this diagram. I need equation to calculate frequency & duty% for this diagram so that I can determine values of resistors and capacitor(c2).
Can any one provide me the equation, pls.
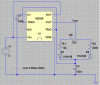
But when I made and tested it practically the ESC (& motor) not running giving err tone. I tested with DMM and found frequency and duty% far from what was demonstrated in Ltspice. I did some trial and err using different values for R1, R2 & C2, finally reached a point where it is working but the running of the motor is not smooth enough.
I want to use this diagram. I need equation to calculate frequency & duty% for this diagram so that I can determine values of resistors and capacitor(c2).
Can any one provide me the equation, pls.