Further to my recent question on magnetics.
I have this coil from a 230v AC octal industrial relay, actually I've a boxfull.
What is the purpose of the copper D shape piece on the pole, the bit where the relay armature would come to rest, looks like a shorted turn.
I suspect it improves effeciency by reducing eddys or similar (the core is solid not laminated), dc relays dont have these.
I was thinking maybe a circular arrangement of these might make a generator, would I be better keeping the copper piece or losing it.
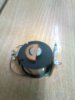
I have this coil from a 230v AC octal industrial relay, actually I've a boxfull.
What is the purpose of the copper D shape piece on the pole, the bit where the relay armature would come to rest, looks like a shorted turn.
I suspect it improves effeciency by reducing eddys or similar (the core is solid not laminated), dc relays dont have these.
I was thinking maybe a circular arrangement of these might make a generator, would I be better keeping the copper piece or losing it.
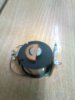
Last edited: