rascupanamuha
Member
Here i am again, with a new project ! Electro scooter
I want to do everything myself. I will connect and program electronic part with arduino
The problem is this:
I have wanted to use this motor: https://www.hobbyking.com/hobbyking...y_RotoMax_1_40_Brushless_Outrunner_Motor.html
And here is what i have calculated so far:
I want max speed of 10m/s
Diameter of wheel: 16cm (circumference=0.5m)
Motor has 228kv, and with 24V battery, that is 5472rmp=91.2 rotates per second
If i want max speed of 10m/s, i should use gear ratio 1:4.55
I dont know what current would it need, and the rest of this...
So what do you think? Is brushless motor goot for this? Or should i go for brushed one?
I am worried if this motor could start scooter with me on it...
Please give me your suggestions
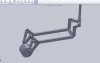
I want to do everything myself. I will connect and program electronic part with arduino
The problem is this:
I have wanted to use this motor: https://www.hobbyking.com/hobbyking...y_RotoMax_1_40_Brushless_Outrunner_Motor.html
And here is what i have calculated so far:
I want max speed of 10m/s
Diameter of wheel: 16cm (circumference=0.5m)
Motor has 228kv, and with 24V battery, that is 5472rmp=91.2 rotates per second
If i want max speed of 10m/s, i should use gear ratio 1:4.55
I dont know what current would it need, and the rest of this...
So what do you think? Is brushless motor goot for this? Or should i go for brushed one?
I am worried if this motor could start scooter with me on it...
Please give me your suggestions

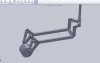