Thanks "
rjenkinsgb" for your insight, I am amazed at the handle you have on electronics, it's great to chat with you on this or anything. I have enjoyed prototyping this little 6 volt generator voltage regulator with you, everything has gone so smoothly unlike other electronic Ideas I have had.
I have worked for Hewlett Packard years ago building Oscilloscopes but I was working as an Electro Mechanic at the time maintaining production equipment did a lot of High Vacuum stuff, Built some controllers and got know everyone and all the Jobs they did building CRT's. I was always a bit of a pain for the bosses as I would design my own electronics for machines rather than get something already made from off the shelf. Then I got into computers doing systems management for HP but that job was really the Building Systems Electronic Tech Job.
After leaving HP I got an Electronic Engineering Job doing High End Home Theater Sound equipment, mostly testing, troubleshooting and repair for the design engineers. That all is in the past. So now it's been a lot of fun for me to play with this Voltage Regulator,
I will post a final schematic with resistor values that will fix the voltage range so it can't burn out the generator etc...
I want to build another one before changing 680 / 1.2K ohm input divider resistor values as thing are just too tight with the prototype..
Will post a final schematic for anyone that wants to make there own when I figure out the Field Start Circuit design whatever it turns out to be. I did order some 2.5 ohm
2322 661 54711 PTC Thermistors to try on the field.
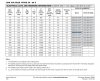
Still need to source a better barrier diode, A TO-247 package with an electrically isolated heat sink contact would be nice, something that did not have much change in forward voltage drop at around 25 Amps.
As always will try your suggestions on input values. Testing is kind of a wild thing to do, the header exhaust on my little 36 horse VW is noisy and the heat from the engine is blowing on me as I rev the engine and try to take readings without getting the voltmeter leads caught in the generator belt. Fun!
Wish you could see the Scope waveforms it's producing, difficult to catch on camera. The amplitude on the gate builds as the engine revs until the generator output voltage becomes stable and the gate pulse amplitude reaches about 4.4 volts. Its ON width varies from just a spike to a over square wave depending on load and RPM. It's still drops out at Idle however it comes back in without having to over rev the engine like it needs the first time stating.
Part of the starting charging problem is this generator, it does this too on the mechanical voltage regulator. The generator seems to lose its residual magnetism, If left more than 3 days.