Among my many "weaknesses", is the lack of ability to actually package a project. I am fine getting a project on a breadboard....and I have a whole bunch of filled breadboards to prove that point. To illustrate, I went looking for a breadboard and found at least seven around here, all populated. To my surprise, I even found one of a binary clock (pictured below) using a PIC16C54. I have a folder with the hand-drawn schematic and a printed code listing...dated 19-JUL-1993! Worked like a charm...still on the breadboard....more than 25 years later. Apparently, I am waiting for this historical artifact to be discovered by future generations where archeologists will debate its cultural significance.
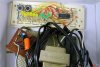
This morning, I was going to drive out to a local place and buy another breadboard. This leads me, hopefully humorously so, to the point of my post. A while ago, I made a project to read and display particulate matter concentrations in air using **broken link removed** A close friend saw this project, which I demonstrated, and wants it to actually use in his shop. As he is a long time friend and colleague, I had it in mind to package it and send it along as a nice holiday gift. I can also reclaim the breadboard! I am asking for help.
So, here is the problem, the stumbling bock, the force that keeps it in place on the breadboard. If you look at the data sheet ( e.g., p4), you will see the air outlet and inlet areas that are used to pull the air sample in and expel it out. I am not finding a case that will exactly fit those dimensions and even if I could, I'm not sure that I could fit the rest of the components as well. I need to route those air ports to the case and I don't know what to use and how to attach them at either end. I want it to be both functional and neat. I just can't slop a bunch of glue onto some makeshift and ill-fitting tubes as it will look like a small child did it in 3rd grade art class.
How would you do it? Be as specific as you possibly can...where do I find square tubing for the exhaust fan and rectangular tubing to fit over the inlet (which is right on the edge of the sensor. What would I use to attach it to both the sensor and the case. How do I make a precision fit such that I could, at least potentially, get back into the project and reprogram as needed and so on?
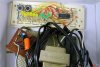
This morning, I was going to drive out to a local place and buy another breadboard. This leads me, hopefully humorously so, to the point of my post. A while ago, I made a project to read and display particulate matter concentrations in air using **broken link removed** A close friend saw this project, which I demonstrated, and wants it to actually use in his shop. As he is a long time friend and colleague, I had it in mind to package it and send it along as a nice holiday gift. I can also reclaim the breadboard! I am asking for help.
So, here is the problem, the stumbling bock, the force that keeps it in place on the breadboard. If you look at the data sheet ( e.g., p4), you will see the air outlet and inlet areas that are used to pull the air sample in and expel it out. I am not finding a case that will exactly fit those dimensions and even if I could, I'm not sure that I could fit the rest of the components as well. I need to route those air ports to the case and I don't know what to use and how to attach them at either end. I want it to be both functional and neat. I just can't slop a bunch of glue onto some makeshift and ill-fitting tubes as it will look like a small child did it in 3rd grade art class.
How would you do it? Be as specific as you possibly can...where do I find square tubing for the exhaust fan and rectangular tubing to fit over the inlet (which is right on the edge of the sensor. What would I use to attach it to both the sensor and the case. How do I make a precision fit such that I could, at least potentially, get back into the project and reprogram as needed and so on?