Here's the LTspice simulation of a 100W, 120V incandescent light bulb empirically derived model that reasonably matches OBW0549's resistance measurements in post #13.
The model does not include any thermal lag that the real bulb would have.
For that reason It also only works for DC voltages, not AC.
Below is the simulation of the 100,000uF cap discharging from 50V through the 100W bulb compared to discharging through a resistor dissipating the same power at 50V.
Note the faster discharge with the bulb due to its non-linear resistance with voltage.
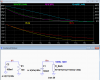
The model does not include any thermal lag that the real bulb would have.
For that reason It also only works for DC voltages, not AC.
Below is the simulation of the 100,000uF cap discharging from 50V through the 100W bulb compared to discharging through a resistor dissipating the same power at 50V.
Note the faster discharge with the bulb due to its non-linear resistance with voltage.
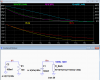
Last edited: