SimonSolar2C
New Member
Hi, I have been trying to design a low cost small circuit to voltage clip off my small 2watt solar cell's 7volt voltage when it is open circuit so my phone will charge off it.
My iPhone charges from 4 to 6.2 volts.
Solar panel is Voc=7v, Isc=280ma
Ideally the solar panel would sit at 7 volts so it doesnt produce current and when the phone connects it "sees" 6.2 volts so it starts charging, pulls the voltage down to start generating current.
I dont think a volatage regulator is required - that is sort of over engineered and I want the solution to be simple that I can build into my cable.
My first idea of a simple zener shunt causes too much heat in the zener.
My second idea uses a transistor, but Im not sure if that is just redundant.
Any suggestions from analogue experts appreciated
Transistor circuit idea:
My iPhone charges from 4 to 6.2 volts.
Solar panel is Voc=7v, Isc=280ma
Ideally the solar panel would sit at 7 volts so it doesnt produce current and when the phone connects it "sees" 6.2 volts so it starts charging, pulls the voltage down to start generating current.
I dont think a volatage regulator is required - that is sort of over engineered and I want the solution to be simple that I can build into my cable.
My first idea of a simple zener shunt causes too much heat in the zener.
My second idea uses a transistor, but Im not sure if that is just redundant.
Any suggestions from analogue experts appreciated
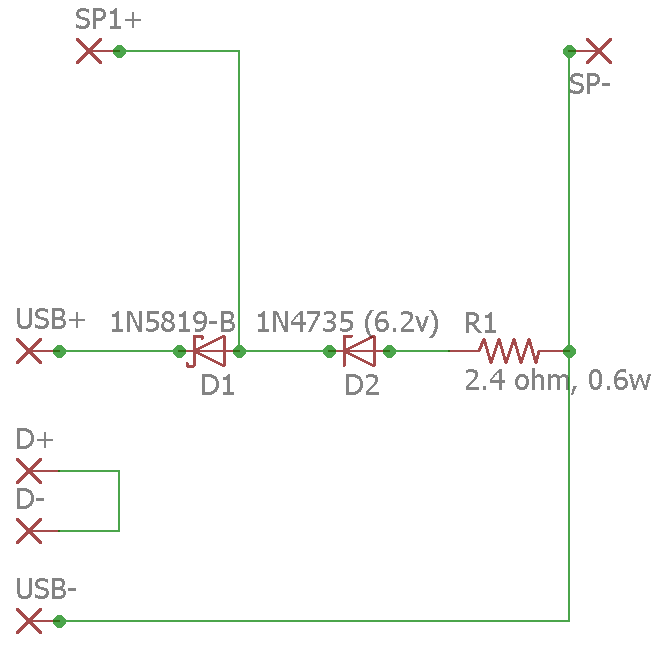
Transistor circuit idea:
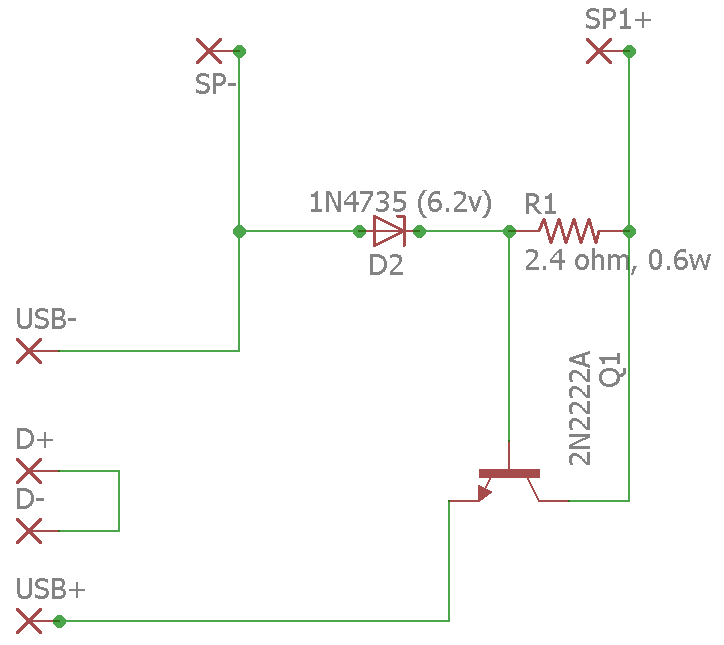