Superman--
New Member
Okay here is the basic issue. (image of current design on bottom)
I have 555 timer PWM multichannel board and I blow MOSFETs like crazy.
So I have imposed a Voltage limiter for the PWM but still blow the MOSFETs.
So the I went to redesign that .
I have new MOSFETs that are 12v 75A each. With single current flow configuration.
So does anyone see any flaws with this design?
Also each MOSFET will run around 40A-60A draw continuance.
And so does anyone have an idea on how to limit the current to the load.
Just so I do not go over 50A. Any input would be appreciated.
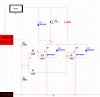
By the way the program I am using says that this will work but cuts out after 15 seconds. It's driving me nuts.
Thanks again in advance.
I have 555 timer PWM multichannel board and I blow MOSFETs like crazy.
So I have imposed a Voltage limiter for the PWM but still blow the MOSFETs.
So the I went to redesign that .
I have new MOSFETs that are 12v 75A each. With single current flow configuration.
So does anyone see any flaws with this design?
Also each MOSFET will run around 40A-60A draw continuance.
And so does anyone have an idea on how to limit the current to the load.
Just so I do not go over 50A. Any input would be appreciated.
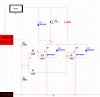
By the way the program I am using says that this will work but cuts out after 15 seconds. It's driving me nuts.
Thanks again in advance.