Hi all,
I am building a DC motor control demonstration panel. Apart from controlling the speed I also want to simulate variable load acting on the DC motor. Hence I thought of coupling another DC motor to the existing one and rotating it in the opposite direction just like in the figure.
If we say that motor A is the motor to be controlled (clockwise) and B is the torque generator, even though B is given power to rotate anti clockwise it will always be rotating in the opposite direction (because of A). This will cause B to heat up and I fear that it would get burnt.
The goal is to somehow dissipate the current generated by B. Can you all help me.
BTW both motors will be driven by H-bridges and both will have speed measuring ability.
Thank you !!!!!!!!!!!!!!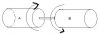
I am building a DC motor control demonstration panel. Apart from controlling the speed I also want to simulate variable load acting on the DC motor. Hence I thought of coupling another DC motor to the existing one and rotating it in the opposite direction just like in the figure.
If we say that motor A is the motor to be controlled (clockwise) and B is the torque generator, even though B is given power to rotate anti clockwise it will always be rotating in the opposite direction (because of A). This will cause B to heat up and I fear that it would get burnt.
The goal is to somehow dissipate the current generated by B. Can you all help me.
BTW both motors will be driven by H-bridges and both will have speed measuring ability.
Thank you !!!!!!!!!!!!!!
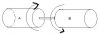