polashd
Member
In the attachments there are two circuits (circuit 01 & circuit 02) which I intent to charge a photo-flash capacitor for zapping Nicad batteries.
I’m confused about the transformer connection to other parts.
In circuit 01 all three coils are winded in the same direction (using right hand technique).
-L1 starts from pin 3 – ends at pin 2
- L2 starts from pin 4 – ends at pin 1
- L3 starts from pin 6 – ends at pin 5
In the diagram I labeled transformer points as A B C D & E
I need help to connect the transformer (ie. Which pin to connect to which point, like pin 2 = point C ….).
In circuit 02 there are 2 coils.
-L1 starts from pin 2 – ends at pin 1
- L2 starts from pin 4 – ends at pin 3
I connected the pins like the diagram.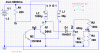
Not yet tested the circuit to be sure that the transformer coil orientation is correct!
I got both the circuits from internet and added the feedback / control system myself.
Is the feedback system correct?
I’m confused about the transformer connection to other parts.
In circuit 01 all three coils are winded in the same direction (using right hand technique).
-L1 starts from pin 3 – ends at pin 2
- L2 starts from pin 4 – ends at pin 1
- L3 starts from pin 6 – ends at pin 5
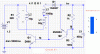
In the diagram I labeled transformer points as A B C D & E
I need help to connect the transformer (ie. Which pin to connect to which point, like pin 2 = point C ….).
In circuit 02 there are 2 coils.
-L1 starts from pin 2 – ends at pin 1
- L2 starts from pin 4 – ends at pin 3
I connected the pins like the diagram.
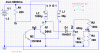
Not yet tested the circuit to be sure that the transformer coil orientation is correct!
I got both the circuits from internet and added the feedback / control system myself.
Is the feedback system correct?