Mikebits
Well-Known Member
I know all of you have come up with clever ways to test, build, or otherwise do something in electronics, either to save time, cost, or just because it was cool. If you have something that you think would benefit the ETO community, or simply because you thought it was nifty. Post it here. Let's see how long we can keep this thread going. I will start off.
The other day, I needed a 1 ohm resistor for a DC circuit I was working on. I did not have one and did not want to wait to purchase one. So I went and rolled my own, resistor that is.
Tip 1.
I had some 32 AWG magnet wire which was about .25 ohm per foot. Did the math, and measured out the right length of wire.
I then needed something to form the wire on, so I took some fiberglass rod I had, drilled holes on each end to insert some 22 AWG leads into and then formed the resistor to a shape on my lathe which would hold the magnet wire in place (of course, you can roll your magnet wire on any other form factor you may have on hand.
Below is my preformed resistor minus the magnet wire.
Once that was done, it was a simple matter of rolling the magnet wire onto the resistor form (I used my lathe as a wire winder to save time).
Once done and not very pretty but was pretty solid, I soldered the magnet wire to the 22 AWG leads I had glued into my resistor form earlier (I think I did not mention that before, now ya know)
I then checked the ohmic value on my trusty Keithley 2010 DMM.
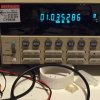
Okay so I have about 3% error, but close enough for my circuit.
Tip 2.
Need a low ohmic value resistor (in milliohm range) for current sensing perhaps? A paper clip has about 20 - 30 milliohm resistance, just roll straightened paperclip on a shaft and you have a milliohm resistor.
(Note: for tips 1 and 2, these DIY resistors have a lot of inductance, so may not work in a high frequency circuit).
The other day, I needed a 1 ohm resistor for a DC circuit I was working on. I did not have one and did not want to wait to purchase one. So I went and rolled my own, resistor that is.

Tip 1.
I had some 32 AWG magnet wire which was about .25 ohm per foot. Did the math, and measured out the right length of wire.
I then needed something to form the wire on, so I took some fiberglass rod I had, drilled holes on each end to insert some 22 AWG leads into and then formed the resistor to a shape on my lathe which would hold the magnet wire in place (of course, you can roll your magnet wire on any other form factor you may have on hand.
Below is my preformed resistor minus the magnet wire.
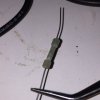
Once that was done, it was a simple matter of rolling the magnet wire onto the resistor form (I used my lathe as a wire winder to save time).
Once done and not very pretty but was pretty solid, I soldered the magnet wire to the 22 AWG leads I had glued into my resistor form earlier (I think I did not mention that before, now ya know)
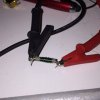
I then checked the ohmic value on my trusty Keithley 2010 DMM.
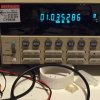
Okay so I have about 3% error, but close enough for my circuit.
Tip 2.
Need a low ohmic value resistor (in milliohm range) for current sensing perhaps? A paper clip has about 20 - 30 milliohm resistance, just roll straightened paperclip on a shaft and you have a milliohm resistor.
(Note: for tips 1 and 2, these DIY resistors have a lot of inductance, so may not work in a high frequency circuit).