HI All,
I need to implement a high side shut resistor based current sensing with a Differential ADC. Here the line consists of around 12VDC @ current varies from 1 to 10A. Eventhough the drop stands within the Differential i/p voltage limit(+/- 2.048V), its common mode voltage is higher than what is allowed.
Also I am aware that, there are some dedicated ICs and Opamp based instrumentation amplifiers are available, I am just trying to implement with same ADC & less components (as shown in the attached image.) . Simulation everything seems good, but before implementing I am seeking some advice from you. Whether this is a good practice for implementation. Hoping for your valuable suggestions.
Thanks in advance
Regards,
Geo
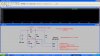
I need to implement a high side shut resistor based current sensing with a Differential ADC. Here the line consists of around 12VDC @ current varies from 1 to 10A. Eventhough the drop stands within the Differential i/p voltage limit(+/- 2.048V), its common mode voltage is higher than what is allowed.
Also I am aware that, there are some dedicated ICs and Opamp based instrumentation amplifiers are available, I am just trying to implement with same ADC & less components (as shown in the attached image.) . Simulation everything seems good, but before implementing I am seeking some advice from you. Whether this is a good practice for implementation. Hoping for your valuable suggestions.
Thanks in advance
Regards,
Geo
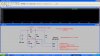