Hi,
I was just trying to implement a Buck-Boost converter with a driver method as shown in the image. Since the IR2110 have individual High side and low side driving, i actually
thought this will help to avoid the using discrete components. But now I came to realize that I was wrong !
The issues I was facing ,
1) Boost operation
For boost operation (ie, switching the LOW side MOSFET Q4 ), the HIGH side MOSFET Q3, normally should be ON for provide the supply . This is not happening because the
Q3 MOSFET is not coming to ON state . I believe its because of the boost strap capacitor is not getting charged , which is usually happening through the LOW side MOSFET's ON
state if its in a HALF bridge circuit .
2) Buck Operation
The Buck circuit normally formed by switching HIGH side Q3 mosfet and keeping the LOW SIDE MOSFET Q4 always in OFF state. I believed atleast this part will work, but its
seen that, till 30% Duty Cycle, the buck part is responding as mentioned above , but after that , the PIC controller is getting heated up and all voltages are diminishing. What
would be happening here ?
The i/p voltage V_PS is just 8-18V & Vout is between 11.5 to 13-5V, and later planning to expand.
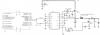
Thank You,
regards,
Geo
I was just trying to implement a Buck-Boost converter with a driver method as shown in the image. Since the IR2110 have individual High side and low side driving, i actually
thought this will help to avoid the using discrete components. But now I came to realize that I was wrong !
The issues I was facing ,
1) Boost operation
For boost operation (ie, switching the LOW side MOSFET Q4 ), the HIGH side MOSFET Q3, normally should be ON for provide the supply . This is not happening because the
Q3 MOSFET is not coming to ON state . I believe its because of the boost strap capacitor is not getting charged , which is usually happening through the LOW side MOSFET's ON
state if its in a HALF bridge circuit .
2) Buck Operation
The Buck circuit normally formed by switching HIGH side Q3 mosfet and keeping the LOW SIDE MOSFET Q4 always in OFF state. I believed atleast this part will work, but its
seen that, till 30% Duty Cycle, the buck part is responding as mentioned above , but after that , the PIC controller is getting heated up and all voltages are diminishing. What
would be happening here ?
The i/p voltage V_PS is just 8-18V & Vout is between 11.5 to 13-5V, and later planning to expand.
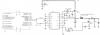
Thank You,
regards,
Geo