This is another of my occasional "show and tell" threads.
While recently working on an RF power amplifier, it occurred to me that it would be useful to be able to monitor the supply current.
The amplifier is powered from 12 volts and draws a current of the order of 10 amps.
Using the current range of the ubiquitous DMM is often awkward.
For my 12v supplies, I use Anderson "PowerPole" connectors, so it would be convenient to have PowerPole connectors built in to a dedicated ammeter.
Looking through my junk box, I found a long dead project which had a small moving coil meter mounted in a diecast box.
A few basic measurements on the meter showed that it had a full scale current of 1mA and a coil resistance of 18.75 Ohm. This corresponds to 18.75mV FSD.
What to use for a shunt to give a useful full scale range of say 20 amps?
On the basis that this was to be a zero cost project, and as far as I know I have no low temperature coefficient resistance wire, I decided to use plain old enamelled copper wire. Probably not the best for temperature stability, but adequate* for what I am trying to do.
Looking through my wire box I found some 18SWG enamelled copper wire.
Looking at some copper wire tables and doing a quick calculation I found that I needed about 8.2cm of wire to give 3.6milli-Ohm for a 20amp shunt.
I cut a length of wire a few cm longer than the required 8.2cm to allow for experiment and adjustment and to make a four terminal shunt resistor.
To calibrate my home made shunt, I used a large commercially made and calibrated shunt resistor in conjunction with my bench DVM to measure the voltage across the commercial shunt while passing a current through the two shunts connected in series.
Using this method I was able to solder two wires on to my shunt in the appropriate places to give the correct current reading on the meter.
The meter scale itself was a bit of a problem. The meter was originally used in some long dead piece of equipment and had a non-linear scale calibrated in dB. Not very useful for my application.
I was about to hand draw a paper scale when I remembered that there is an application somewhere in the interwebs which can be used for printing meter scales.
After a bit of searching I found it, it is called GALVO, as in Galvanometer.
EDIT: Ooops! WRONG, it is called GALVA rather than galvo.
It was originally written in French, but there is an English user guide and version which has mostly English commands.
Anyway, after all this waffle, here it is:
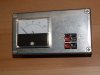
And inside:
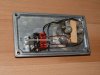
My home made shunt can be seen extending out to the righthand side of the red terminals, and bent into a hairpin loop.
So there it is.
The solder connections to the meter look as though they could do with tidying up a bit.
The hole in the box where the connectors protrude is a bit on the big side. A classic case of measuring very carefully and still getting it wrong!
I also need to make a label for the connectors to show which is IN from the supply and which is OUT to the load, otherwise the meter deflects the wrong way (obviously), making another source of annoyance at busy times on the workbench.
JimB
* As per Eric Gibbs signature line "Good enough is perfect"
While recently working on an RF power amplifier, it occurred to me that it would be useful to be able to monitor the supply current.
The amplifier is powered from 12 volts and draws a current of the order of 10 amps.
Using the current range of the ubiquitous DMM is often awkward.
For my 12v supplies, I use Anderson "PowerPole" connectors, so it would be convenient to have PowerPole connectors built in to a dedicated ammeter.
Looking through my junk box, I found a long dead project which had a small moving coil meter mounted in a diecast box.
A few basic measurements on the meter showed that it had a full scale current of 1mA and a coil resistance of 18.75 Ohm. This corresponds to 18.75mV FSD.
What to use for a shunt to give a useful full scale range of say 20 amps?
On the basis that this was to be a zero cost project, and as far as I know I have no low temperature coefficient resistance wire, I decided to use plain old enamelled copper wire. Probably not the best for temperature stability, but adequate* for what I am trying to do.
Looking through my wire box I found some 18SWG enamelled copper wire.
Looking at some copper wire tables and doing a quick calculation I found that I needed about 8.2cm of wire to give 3.6milli-Ohm for a 20amp shunt.
I cut a length of wire a few cm longer than the required 8.2cm to allow for experiment and adjustment and to make a four terminal shunt resistor.
To calibrate my home made shunt, I used a large commercially made and calibrated shunt resistor in conjunction with my bench DVM to measure the voltage across the commercial shunt while passing a current through the two shunts connected in series.
Using this method I was able to solder two wires on to my shunt in the appropriate places to give the correct current reading on the meter.
The meter scale itself was a bit of a problem. The meter was originally used in some long dead piece of equipment and had a non-linear scale calibrated in dB. Not very useful for my application.
I was about to hand draw a paper scale when I remembered that there is an application somewhere in the interwebs which can be used for printing meter scales.
After a bit of searching I found it, it is called GALVO, as in Galvanometer.
EDIT: Ooops! WRONG, it is called GALVA rather than galvo.
It was originally written in French, but there is an English user guide and version which has mostly English commands.
Anyway, after all this waffle, here it is:
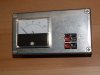
And inside:
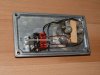
My home made shunt can be seen extending out to the righthand side of the red terminals, and bent into a hairpin loop.
So there it is.
The solder connections to the meter look as though they could do with tidying up a bit.
The hole in the box where the connectors protrude is a bit on the big side. A classic case of measuring very carefully and still getting it wrong!
I also need to make a label for the connectors to show which is IN from the supply and which is OUT to the load, otherwise the meter deflects the wrong way (obviously), making another source of annoyance at busy times on the workbench.
JimB
* As per Eric Gibbs signature line "Good enough is perfect"
Last edited: